Cutting metals and steels at high temperatures using a thermal cutting process: How can such a job be done sustainably? Breuer Metallbearbeitung GmbH from Bad Laasphe in the Wittgensteiner Land region would like to produce its own hydrogen for this purpose.
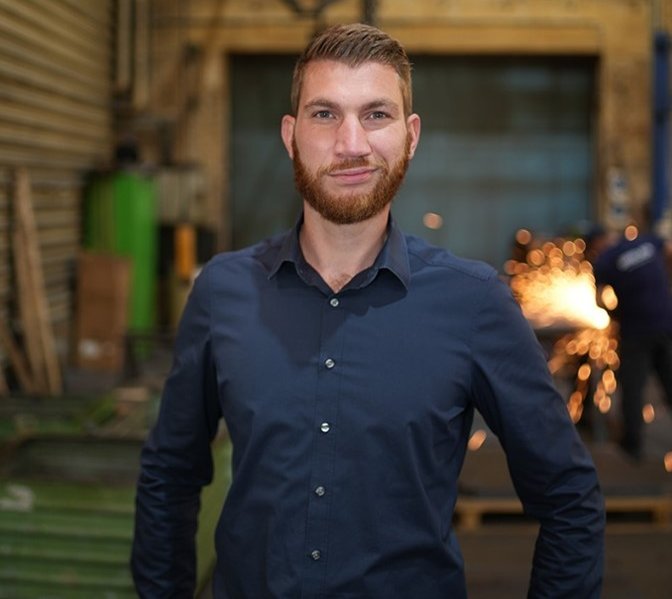
“We burn for our customers” is the claim with which Breuer Metallbearbeitung GmbH advertises on its website. The sentence precisely describes the business model of the 32-employee company: the medium-sized company from Bad Laasphe in Westphalia is at the interface between steel manufacturers and the metalworking industry. “We receive steel plates from the rolling mill or the steel trade, separate and process the material and deliver finished blanks to the steel, machine or tool construction industry,” explains owner and Managing Director Bernhard Ständer. The customer base mainly includes companies from the region. Punching tool and steel construction companies in particular need tailor-made steel blanks. “If required, we can also take care of work steps such as milling or sandblasting,” says Ständer.
The process that Breuer mainly uses to cut the steel plates is called oxy-fuel cutting. It has been in use for more than 100 years. For just as long, metalworkers have been faced with the challenge of completing this step in the most resource-efficient way possible. The problem: in order for steel to be cut, it has to be heated to temperatures of over 1,000 degrees Celsius at certain points. In addition to oxygen, this requires fuel gases such as propane or acetylene - and these release a lot of CO2. “We also use alternative processes such as plasma or laser cutting,” explains Ständer. “But these also consume a lot of energy or are not economically viable above certain sheet thicknesses.”
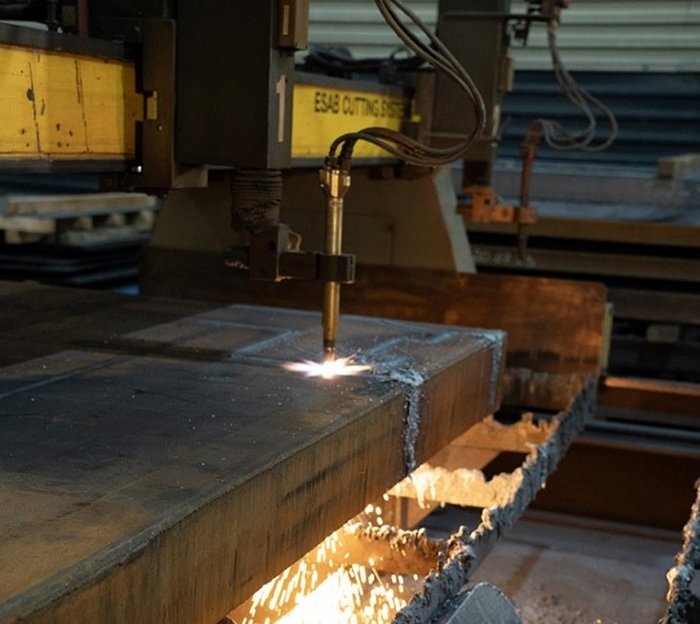
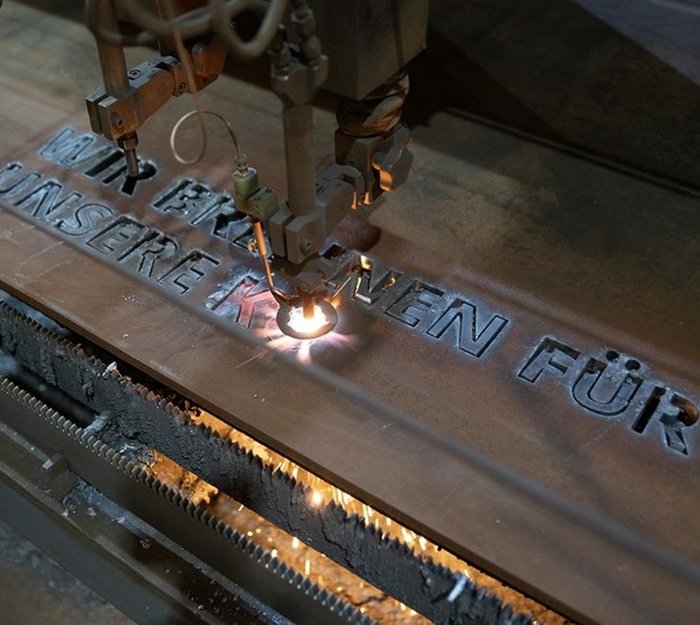
The biggest CO2 lever: the switch to hydrogen
The young Managing Director took over the company in July 2021. The topic of sustainable transformation has been on his mind from the very beginning, he says: “I personally think it's important that we get our environment and our climate under control - for my children and myself.” But reducing CO2 emissions is also key for companies. “I believe that German industry only has a chance if it moves towards climate neutrality.”
The medium-sized company from the Wittgensteiner Land region has therefore set itself an ambitious goal: The company wants its production to be climate-neutral by 2030. But exactly how many emissions are produced in a metalworking company? And where can they be reduced and how? “We are currently working with an energy consultant to draw up our first carbon footprint,” says Ständer. “There are a few requests for this. Very few, but it is definitely an issue among our customers and suppliers. And our customers have also already indicated that they want to do more in this area in the future - which means we also have a role to play.”
All possible aspects are recorded in the balance sheet: from the supply chain to all work steps and logistics. However, which steels are processed at Breuer depends on the customer's wishes. “We use the certificate to see where the steel comes from,” explains the Managing Director. “Of course, there is already green steel on the market. But from what I hear, hardly anyone wants it at the moment - because it's still too expensive.” It is difficult for a single medium-sized company to influence this, says Ständer. That's why, when it comes to transformation, the focus is on the adjustments that can really be made. And for a company that produces flame-cut blanks, these are primarily the climate-damaging fuel gases.
The Managing Director has a specific idea for avoiding them: “We would like to replace the propane with green hydrogen.” Technically, that would be possible. The problem is availability: there is currently not enough hydrogen in Germany, nor will Bad Laasphe be connected to the future core network in the foreseeable future - according to current plans, a conversion pipeline runs northwest along the Rhine route and the connection to the Ruhr area. “That's why we want to produce the hydrogen ourselves,” says Ständer.
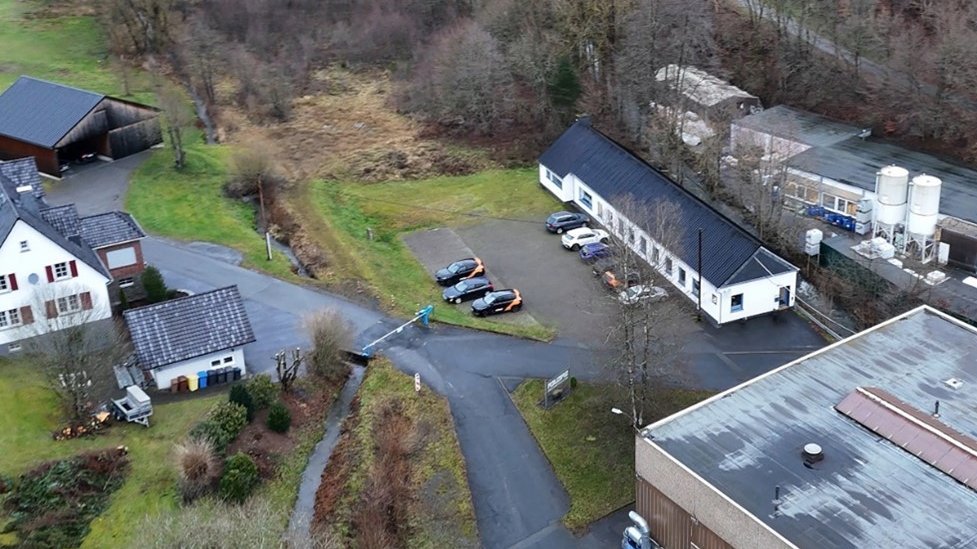
Electrolysers, permits and the price of electricity: there are still many question marks
The entrepreneur would like to use a 7,500 square meter open space right next to the company headquarters for this purpose. “It has been lying fallow for years and is officially agricultural land. If I had permission, I would apply for a huge solar power system for it today and we would have endless electricity - for us and our hydrogen production.” A system with around 750kW peak could be installed on the site, says Ständer. “This would allow us to generate 750,000 kWh of clean energy per year - and probably between 9,375 kg and 18,750 kg of hydrogen.”
The plan is there, but implementation has been bumpy so far. “Obstacles are being put in our way everywhere,” complains Ständer. One problem is the development plans for the planned area. Another is transformation expertise. “Small SMEs like us actually need someone to support them and see how we can help in individual cases, especially with the bureaucratic hurdles.”
The Managing Director has already acquired a lot of knowledge himself: in discussions with the Chamber of Industry and Commerce, energy consultants and flame-cutting manufacturers. “We have sought advice on what we would have to change in our flame-cutting machines in order to switch to hydrogen - the investment would not be too great,” says Ständer. A small manual flame-cutting machine would even be purchased soon. “We could use it for simple cutting tasks and run it on hydrogen.” They are just waiting for funding.
Another topic is the electrolyzers needed for H2 production. “A lot is still under development,” says the company owner. “At the moment, there are almost only start-ups and no suppliers who can offer market-ready products with certainty.” The price development is also difficult to calculate: “Once the solar system is up and running, the question arises: what is the most sensible use for the electricity? Do I produce hydrogen from it or feed it into the grid? In the end, it may also turn out that hydrogen production is not worthwhile at all,” says Ständer. Small companies that do not have access to large sustainability departments often feel lost in the jungle of approvals and subsidies. According to Ständer, it would be helpful to have an advice center that provides support with applications and draws up a roadmap of what needs to be done and in what order: “The complex approval procedures are a problem for us. We have too little knowledge and too little time to deal with the details.”
But despite all the challenges, Breuer's determination to drive forward the sustainable transformation is unbroken. “I hope that our transformation concept will be ready by the summer,” says Managing Director Ständer. The roof should be renovated and the photovoltaic system installed on the roof by the end of 2025. “The future definitely lies with hydrogen,” says Ständer. “The only question is when and how the transition will succeed.”
About the company
Breuer Metallbearbeitung GmbH is a metal processing company from Bad Laasphe. With its 32 employees, the company mainly produces flame-cut parts in material thicknesses of 1 to 300 millimeters for toolmaking, mechanical engineering and steel construction at two locations. Oxyfuel flame cutting, laser cutting and plasma cutting technologies are used for this purpose. Milling, grinding and sandblasting are also part of the portfolio. More information: https://breuer-metall.de